Roberval
Sand Casting | CNC Machining
An exploration of CNC machining and sand casting, Roberval riffs on the design of classic weighing scales.
Materials.
| Aluminum 356
| Everdur Silicon Bronze
| Cherry
| UHMW (pattern board)
| Polyurethane (pattern board)
| Purchased hardware
Processes.
| CAD modeling (Solidworks)
| CAM programming (HSM Works)
| CNC milling (Haas VF2, ShopBot)
| Pattern making
| Sand casting
| Manual milling
| Hand finishing
Timeline.
| 3 weeks
Context.
As part of a 2-person team for the class “ME 365: Making Multiples: Sand Casting,” I worked with Elliot Helms to ideate, prototype, fabricate, iterate, and finish Roberval on a tight, 3 week timeline. For this project, I was directly responsible for prototyping, overall design aesthetic, FEA analysis of our design, CNC machining 2/3 pattern boards, CNC post machining and manual post-machining the bronze base, and hand woodworking.
Design.
Our design goals were to create a beautiful and functional mechanism using multiple, identical parts which we cast simultaneously from family pattern boards. We incorporated both bronze and aluminum castings while also designing for CNC post-machining for high precision and tight-tolerance press-fit features. The simple linkage mechanism and the name pay homage to a centuries-old weighing scale designed by the mathematician Gilles Personne de Roberval.
Manufacturing.
We CNC routed and milled patterns out of obomodulan® 700 PU board and TIVAR® 1000 UHMW. The patterns were fixed to pattern boards by hand, after which we rammed up green sand molds and poured both bronze and aluminum castings. We CNC post-machined all castings, designed for kinematic fixturing, held tolerances tolerances of around +/-.001” for press fits. We CNC routed the cherry trays and hand built the cherry stand. We assembled custom parts with purchased bearings and fasteners on a custom-built jig.
Final CAD model of our scale assembly.
Exploded assembly model highlighting off-the-shelf components for which we designed.
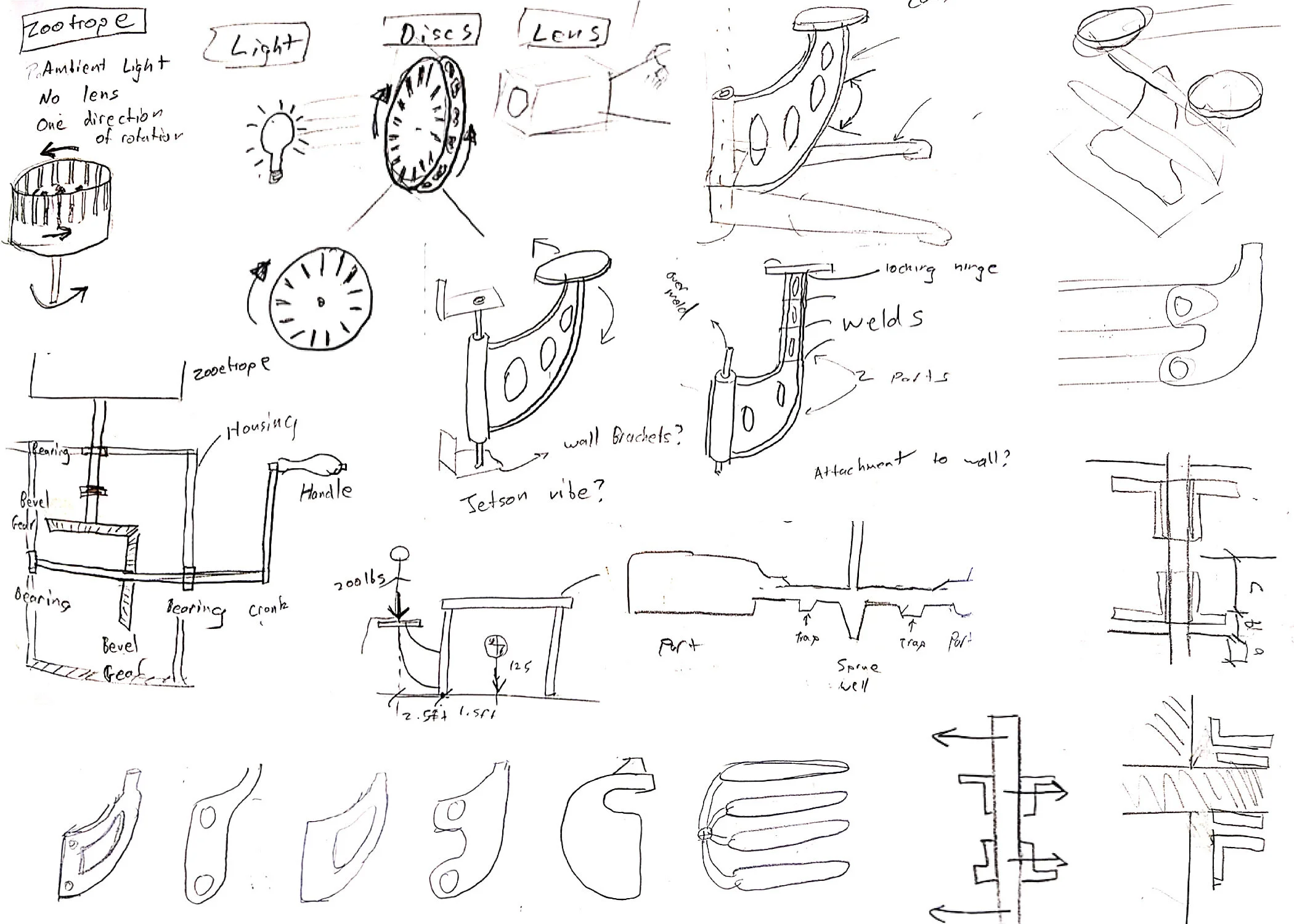
A collection of sketches that I used for generating ideas, exploring design aesthetics, visualizing fabrication processes, and back-of-the-envelope calculations.
Rapid prototyping with laser cut parts, roller bearings, and small, calibrated "weights."
CNC milling the cope and drag side parts of a family pattern board out of UHMW (ultra high molecular weight).

Two-sided pattern made of CNC routed Modulan, to be cast out of bronze for the dense base of the scale.

One-sided family pattern made of CNC milled HDPE for the four cross links, to be cast out of Aluminum 356.

Two-sided family pattern made of CNC milled HDPE for the vertical links, to be cast in Aluminum 356.
Mold for casting the bronze base of the scale. Note the radiating air vents and sprue hole in the lower right
Raw bronze castings of the base with gate, runner, and pouring cup still attached.

Mold for casting the vertical aluminum links with air vents.
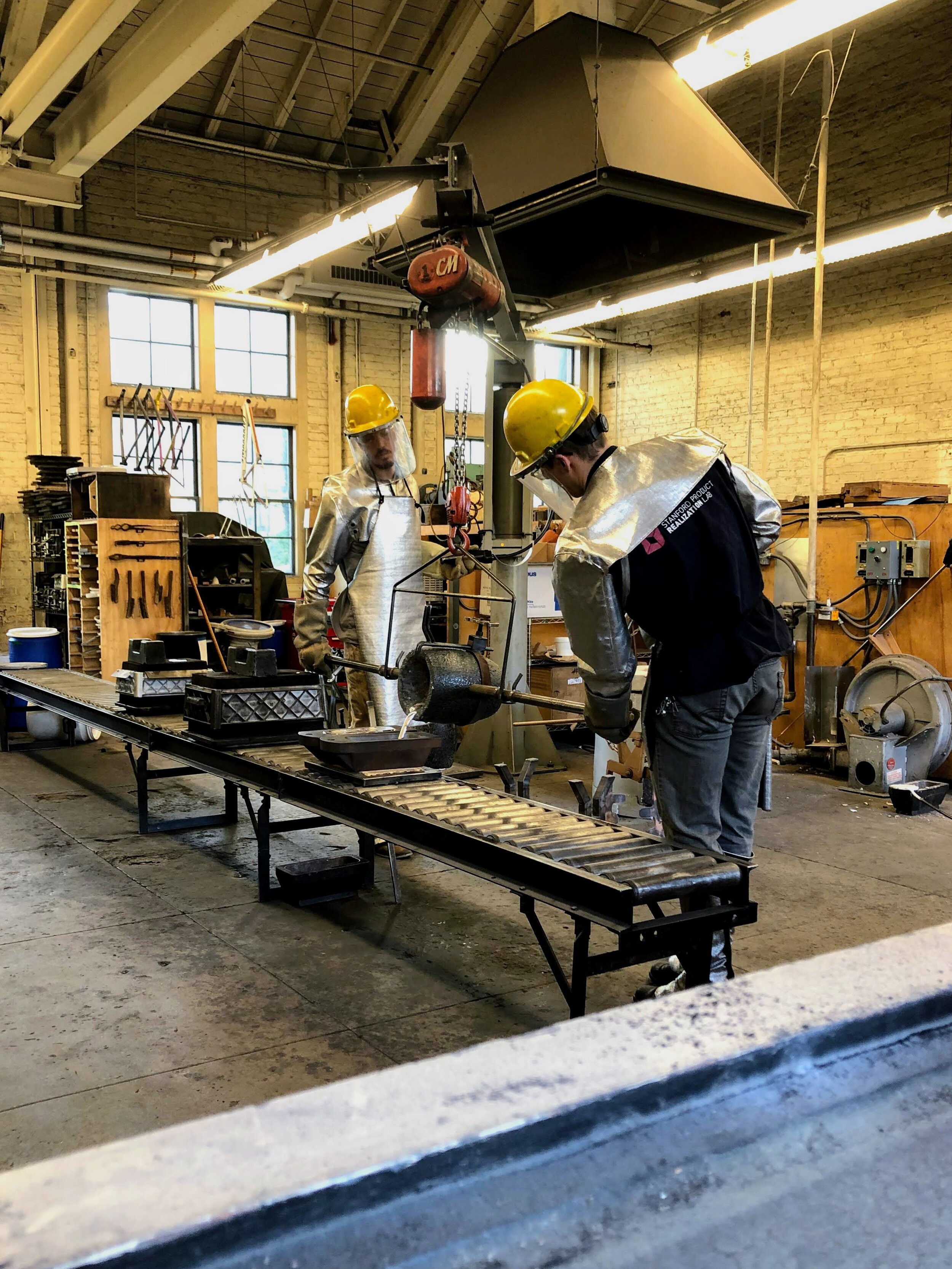
Me pouring aluminum castings with a co-worker (Manu Garzaron).
Molds with weights, fire jackets, and full pouring cups from a recent aluminum pour.
Fixture for compliant constraint and repeatable CNC post-machining of the vertical links.
Vertical links cast in Aluminum 356.
Horizontal links cast in Aluminum 356.

The base cast in Everdur Silicon Bronze.
Short shot part defects on the horizontal links.
Sink defect around the through hole on the horizontal links.
Jig for kinematic constraint of bronze base for repeatable, precise CNC post-machining.
Using a go/no-go plug gauge to measure a bore hole for a bearing press fit. Because of variability in our shop CNCs, we designed these parts with steel safe machining in mind. Progressive machining operations removed material until we reached a hole size of .497"(+.001-.000).
Manual milling in progress on the bronze base. Note the slots that we designed intentionally for fixturing purposes.

FEA and flow analysis for the horizontal links.